Byron Center High School senior Trevor Hofman’s specially designed sprockets will help electric cars zoom around the Berlin Raceway, in Marne. The sprockets’ interior is embellished with dog bone and paw print-shaped cutouts, in honor of the Bulldog mascot.
“I added my own little flavor to it,” he said.
Trevor’s work to create an interchangeable sprocket, a mechanical part that meshes with a chain or track to make a wheel turn, is one of many parts being produced in the electric car class.
Student Inventor Solves Battery Crisis
There was a problem in the Byron Center High School Electric Car class. For students to get the best results when racing their electric cars at Berlin Raceway, the batteries they used needed to be more consistent. Even in deep-cycle batteries of the same model and size, lifespan varies as much as 15 minutes, which is huge in the 60-minute National Electric Car Association race, held in May. Coby Babbs identified the issue: There needed to be a way to determine the actual power of the battery to figure out how long it would last so students know which batteries to install. Coby invented a battery discharge station, where students can determine the strength of each battery. When hooked up to the discharger, gauges record the power level of the batteries, which students record. Once recharged, the batteries are fully re-powered. He even built a cart for it to sit on, welding parts together. “There’s nothing really out there like this,” said Kobe, a senior. “It takes the energy out of the batteries to show us how much energy is in them, so we know which are the best batteries.” |
The class operates more like a small tool and die or car part manufacturer than a high-school classroom.
Machines buzz and sparks fly as students work in teams to perfect their vehicles. Machinery includes two tool room CNC mills, recently donated by Grand Rapids Community College, and a 3-D printer.
In May, juniors and seniors will race their five electric cars against teams from other schools in the National Electric Car Association race. The car that finishes the most laps in 60 minutes is the winner.
“It’s really a race in endurance,” said Logan Thomas, a senior who is in his second year of the class. “It’s about efficiency and speed at the same time. This year we are really focusing on aerodynamics, so we are re-designing our bodies.”
Students use their knowledge from math, physics, computer-aided drafting and computer-aided manufacturing/computer numerical control (CAM CNC) classes to make the parts and assemble them. Work carries over from one year to the next, as students focus on refining designs to make the little automobiles they drive better and faster.
Always Improving and Modifying
It’s highly technical work that requires incredible precision. If one piece is off just a fraction, nothing works, students explained. It’s a matter of trial and error to get things right.
“It’s really a hands-on thing,” Logan said. “Everything I’ve learned in physics and chemistry, I can apply it to what’s happening with the cars.”
Taught by longtime teachers Lary Shoemaker and Marc Cisco, the class is part of the NECA Racing Program, for which teams of students compete from different schools including from Montcalm ISD, Coopersville, Stevensville, Westshore Community College and even schools from Iowa and Montreal.
What students are pulling off each year really hits home on race day, the teachers said. Before that, there are the day-to-day details to focus on, the step-by-step build process.
“The class itself is simply a platform for them to problem-solve,” Shoemaker said. “It really answers that old question we’ve (heard) asked so many times, ‘Why do I need to know this junk?'”
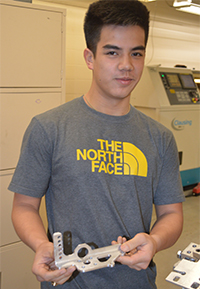
The class has been offered at Byron Center High School for about 15 years, and students are continually creating a bigger foundation for the next class to start with.
This year, the focus is to make car bodies longer and shorter, so there’s not as much drag on the car. They are also moving batteries to the front of the cars to even out weight distribution and are learning the importance of interchangeable parts.
“We are trying to standardized parts,” said Logan, who wants to be an aerospace engineer. “If something goes wrong on one car on race day, we can use another piece. That’s really nice: interchangeability.”
Senior Tommy Nguyen was busy working on a mount to support his car’s brakes, spindle and pitman arm. He explained that new brakes and a steering system have meant he needed to tweak other car parts and configurations. He said that’s part of the fun.
“I honestly have never had another class where I want to stay after school and come in here and work,” said Nguyen, who also wants to be an aerospace engineer. “I want to go that extra mile.”
CONNECT