Each school year in their high school workshop, students build and fine tune electric cars, designing them to be as fast as possible and ready to race.
This year, junior Esme Lowry and seniors Mitchell Mulder and Caiden Bazuin paid extra close attention to a car part they’ve been busy testing — the wheel bearings. The three mechanically inclined students built a makeshift dynamometer to test the bearings and how long car wheels spin — or freewheel — without help from an engine.
“We want the bearing to increase the efficiency of the wheels,” Esme said, explaining how their mobile machine includes two large batteries, a motor and a controller.
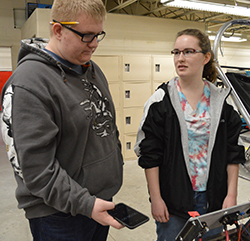
“It was trial and error with making different components and seeing what worked and didn’t work,” Caiden said.
The students are in teacher Lary Shoemaker’s class where each year students build, tweak and ready cars for competitions, hosted by the National Electric Car Association in May. The goal is to have a car go the most laps in 60 minutes. (This year’s races were canceled due to the coronavirus outbreak and state-mandates school closure.)
To demonstrate, the students started up their machine, which was connected to one of the electric cars, setting the rear left wheel into motion. They measured the rotations per minute (RPM) on the machine’s monitor until it hit 400, then shut the machine off, timing how long the wheel spun until it stopped.
They want all four cars to freewheel as long as possible — for the same amount of time, about three to four minutes. A manufacturer donated the high-efficiency bearings. “The new bearings are about three times as efficient as the old ones,” Esme said.
Mitchell explained, “We are hoping because the bearings are better and will freewheel longer they will roll further down the track, and that way we will use less battery and we can get more laps in.”
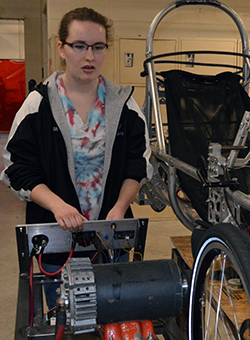
Part of a Car-Making Company
Students said the class gives them the opportunity to focus on areas of improving the cars they are interested in, meaning they learn a lot of different things. The class is more like a company, with students working on different components to build an end product.
“I enjoy the hands-on learning and being able to use different tools and get the creative aspect of being able to design and build different parts,” Caiden said.
Shoemaker said he sets goals with the class each year. “One of our overarching goals this year was to improve efficiency in the car. One area we’ve never spent much time on this year is the wheel bearings, a very vital part of the car.”
Students came up with the idea to make the machine to test the bearings.
“I’m very excited about the fact that we had this idea– to make sure we were applying the same measure from car to car and from wheel to wheel on each car,” Shoemaker said. “It will help us set a benchmark and a standard, and we can also start tracking that information from year to year. If we have a bearing that’s starting to fail, we’ve got a standard. We never had that before.”